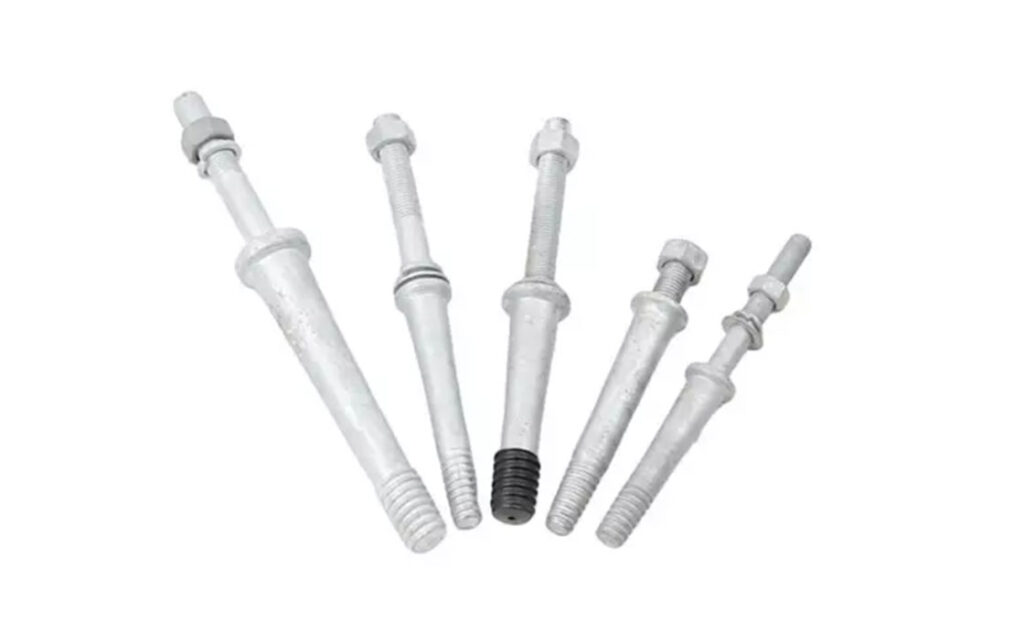
An insulator pin or pin is a component used to support and insulate electrical conductors made from metal. It helps to maintain a physical and electrical separation between the conductor and the structure. This is to prevent electrical current from flowing to the unwanted areas. This helps ensure the safe and efficient operation of high-voltage power lines. Their design and material help to meet the specific requirements of the transmission line. Common types of insulator pin include straight insulator pin, bolted insulator pin, angle insulator pin. They find use in applications such as transmission lines, distribution lines, telecommunication lines, industrial applications and renewable energy projects.
Key features of insulator pin
The insulator pin has various features that contribute to their effectiveness and efficiency. The features vary depending on the system requirements, voltage levels and environmental conditions. Additionally, it is advisable to consult with the industry experts to ensure proper selection of the insulator pin. The following are the key features of the insulator pin.
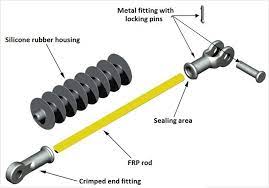
- Material – they are from porcelain, glass or composite materials with high dielectric strength. These materials help them to withstand the electrical stresses imposed by high-voltages.
- Design – insulator pins have a threaded top portion that attaches to the conductor or insulator and a flange top portion.
- Attachment – the pin threads at the top to accommodate the attachment of insulators or conductor clamps. The conductor secures to the pin using suitable hardware to ensure a reliable connection.
- Insulation – the pin prevents electrical current from flowing down the structure to the ground. This is by maintaining a gap or insulation distance between the conductor and the supporting structure.
- Dielectric strength – the dielectric strength is the ability to withstand high electric stresses. It does this without breaking forces caused by wind and allowing electrical arcing.
- Mechanical strength – mechanical strength to support the weight of the conductor. It also helps withstand the mechanical forces caused by wind, ice and other environmental factors.
- Installation – insulator pins install on utility poles or transmission lines at regular intervals. This is to ensure proper spacing and support for the conductors and insulators.
- Maintenance – regular maintenance of insulator pins help to ensure their continued effectiveness.
Selection and maintenance of insulator pins
Selection process should ensure the safe and reliable operation of overhead electrical systems. Proper selection enhances the pins’ contribution to the integrity of the electrical infrastructure. It also helps prevent electrical faults. The factors to consider include voltage level, material, pollution level and corrosion resistance. The installation process should adhere to manufacturer guidelines, industry standards and safety procedures. This is to ensure the integrity of the electrical infrastructure. The following is a basic is a guide on the installation of insulator pin.
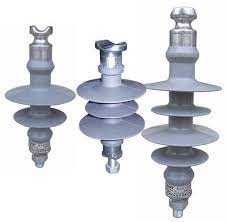
- Safety precautions – ensure that all personnel involved in the installation have proper trainining. Also, ensure they are fully equipped with appropriate personal protective equipment.
- Positioning – determine the correct positioning and height at which the insulator pin should install. Ensure the pin’s height and clearance should meet system requirements and regulations.
- Attachment method – use the suitable attachment method such as threading the pin and into the insulator.
- Insulator or conductor attachment – attach the insulator or conductor to the top of the insulator pin. Ensure secure attachment and alignment of the conductor or insulator string.
- Alignment and positioning – verify the pin aligns and positions according to design specifications.
- Inspection – conduct a visual inspection to ensure that the installation hasis complete. Check for any loose fasteners, misalignment, or other issues.
- Tightening – double-check the tightness of the fasteners and make any adjustments. This is to ensure they are securely fastened.
- Documentation – keep detailed records of the installation including dates, location and any measurements taken during and after installation.
Maintenance and inspection of insulator pin
Insulator pins require regular maintenance and inspection to ensure safe and reliable operation of overhead electrical systems. This helps identify and address issues early. This also helps prevent potential failures or electrical disturbances. Maintenance and inspection helps prevent problems related to insulator pins. This includes flashover, electrical faults and disruptions in electrical service. Additionally, the frequency of inspections varies depending on environmental conditions, pollution levels and criticality of the equipment. The following is a basic guide on the maintenance and inspection of the insulator pin.
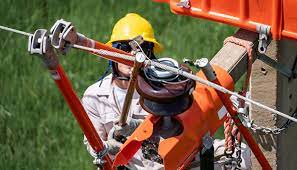
- Conduct routine inspection of insulator pins to check for visible signs of damage contamination or wear.
- Remove any dirt, dust or pollution that may accumulate on the surface of insulator pins. Use a soft, non-abrasive cloth or sponge or a mild cleaning solution.
- Examine insulator pins for signs of corrosion especially in regions with harsh environmental conditions.
- Ensure the insulator pins securely attach to the supporting structure. Check for loose or missing bolts, nuts or fasteners and tighten them as needed.
- Verify the insulator pins align correctly to support the conductor and any attached hardware.
- Inspect the insulators for cracks, chips or other signs of damage.
- Consider implementing pollution control measures to prevent contamination buildup on insulator surfaces.
- Consider performing dielectric testing on insulator pins and insulators. This also helps to assess their electrical integrity.
- Keep detailed records of inspections, cleaning activities and any maintenance or replacements performed.
- Replace any pins with signs of wear, damage or electrical degradation.
Comparative analysis of insulator pins in Southeast Asia
A comparative analysis involves assessing the usage, type, materials and other factors. These factors also influence their application. It also involves comparing the different designs, types and uses in the Southeast Asian markets. The analysis varies depending on the environmental conditions, regulatory requirements and technological advancements. The following are the factors to consider during the comparative analysis in Southeast Asia.
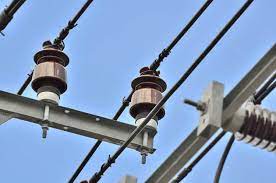
- Usage and applications – insulator pins are mostly used in electrical transmission and distribution systems, supporting conductors and insulators. They also work in renewable energy sources like solar and wind power to support the wiring and cabling systems.
- Types of insulator pins – there are various types of insulator pins used in Southeast Asia. They help to enhance the usability in the environmental conditions in the regions. Some of these types include standard designs, composite insulators and vibration damping pins.
- Material selection – common materials include porcelain and composite materials. These materials have proven their reliability and performance in such environmental conditions.
- Environmental factors – the tropical climate with high humidity and UV exposure influences the material selection and maintenance practices.
- Regulatory and safety standards – some of these countries have standards the insulator pins need to adhere to. These standards include those set by the international electrotechnical commission.
- Manufacturers and suppliers – there are various local manufacturers producing insulator pins. These pins should meet regional demand.
- Environmental sustainability – this involves selecting insulator pins and materials that align with sustainability goals. This helps to minimize environmental impact.
Certifications and standards in Southeast Asia
There are various certifications and standards aligning with insulator pins in Southeast Asia. The standards help to ensure compliance with the relevant standards and regulations. Some of these standards are specific to the regions and intended application. This helps ensures the safety and reliability of electrical systems in Southeast Asia. The following are the common certifications and standards in Southeast Asia.
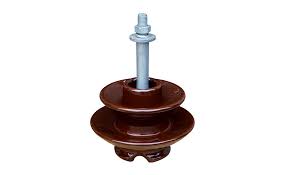
- IEC standards – this standard provides specifications and test methods for insulators.
- National standards and regulations – the different countries have their own national standards and regulations related to electrical equipment and insulator pins.
- Industry-specific standards – there are various industry-specific standards or guidelines influencing insulators pins. It includes requirements related to mechanical strength and pollution resistance.
- ISO certifications – this standard ensures the manufacturer follows the standardized quality processes.
- Local regulations and certification bodies – some countries have their own certification or regulatory agencies responsible for certifying electrical equipment.
Regional markets for insulator pin in Southeast Asia
There are various factors that influence the regional market for the insulator pins in Southeast Asia. These may include the growing electrical infrastructure, urbanization and industrialized in the region. The suppliers and manufacturers should stay informed about the specific demands and opportunities. This is due to the versatile market in Southeast Asia. The following are the common factors that influence the regional market in Southeast Asia.
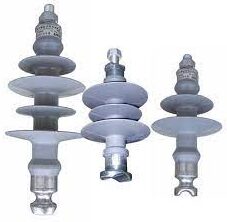
- Infrastructure development – the expanding and upgrading of electrical infrastructure requires new transmission lines, substations and distribution networks.
- Urbanization – rapid urbanization in the region leads to the increased demand for electricity. This also needs the reliable and efficient electrical distribution systems.
- Renewable energy integration – these renewable energy projects involve the installation of new transmission and distribution lines.
- Electrified transport – electrified railway systems require the use of insulator pins. This is to support the overhead catenary wires.
- Electrical grid upgrade – aging electrical grids require modernization and upgrades. This includes replacements of old insulator pins with newer, more reliable designs.
- Safety and reliability – ensuring the safety and reliability of electrical systems to drive the demand for high-quality insulator pins. This helps drive the demand for high-quality insulator pins that meet international and local standards.
- Technological advancements – advancements in materials and manufacturing processes have led to the development of more durable and efficient insulators pins. This is attractive to utilities and infrastructure developers in the region.