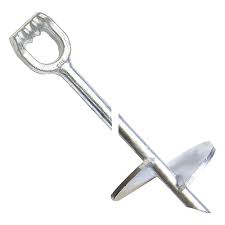
A no wrench screw anchor is a type of anchor used in the construction and maintenance of overhead transmission lines. it has a helical screw designed to provide a secure and stable foundation for utility poles and transmission towers. This is without the need for wrenches or other specialized tools during installation. It is also known as a no wrench helical anchor or helical screw anchors. It is from corrosion-resistant and durable materials. They help to ensure the long-term reliability especially in outdoor and exposed environments. This is particularly helpful in the diverse weather conditions of Southeast Asia such as coastal and tropical climates. The common types include guy anchor, helical pile and rock anchors among others. They find use in various applications such as transmission lines, utility poles, guyed towers, solar panel installations and marine and coastal structures.
Key features of no wrench screw anchor
No wrench screw anchor shave various features that make them versatile and effective for anchoring various structures. They help them work in various soil structures and conditions. The following are the key features of the no wrench screw anchor.
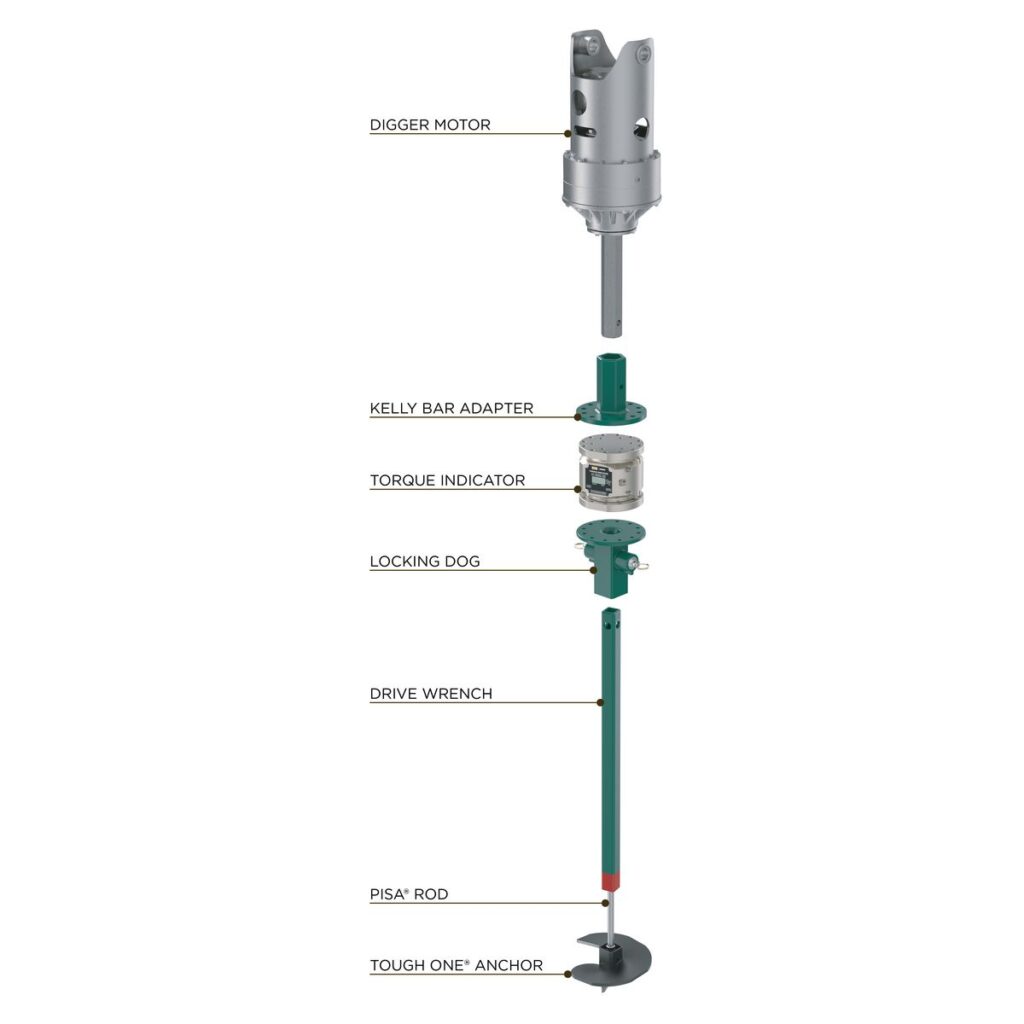
- Helical design – the helical or screw-like shape design allows them to be easily screwed into the ground.
- Load bearing capacity – they help provide excellent load-bearing capacity which suitable for anchoring structures.
- Corrosion resistance – it is from materials that resist corrosion to ensure long-term durability in outdoor environments.
- Minimal soil disturbance – the installation process of the anchor minimizes soil disturbance compared to traditional anchoring methods.
- Adaptability – some of the anchors are expandable which allow them to adapt to various soil conditions. This feature enhances their stability and load bearing capacity.
- Variety of types – there are several types of no wrench screw anchors foe specific applications in the industry. They may work as guy anchors, helical pipes and small-diameter anchors.
- Cost effective – the versatility, ease of installation and adaptability help to save on costs in terms of labor.
Selection and installation of no wrench screw anchor
There are various factors to consider when selecting the no wrench screw anchors for your application. these factors include soil conditions, load requirements, environmental considerations and the type of structure to anchor. The installation should ensure stability and long-term reliability of the anchor. The following is a basic installation guide for the no wrench screw anchor.
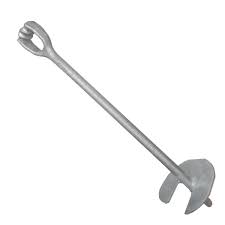
- Preparation – clear the installation area of any obstruction or debris. Mark the locations to install the anchors ensuring they are spaced and aligned correctly.
- Positioning – position the anchor at the determined location and ensure the anchor is vertically aligned or angled as needed.
- Starting the anchor – insert the turning rod or bar into the anchor’s drive socket at the top.
- Installation – turn the anchor in a clockwise direction to initiate the penetration into the ground. Follow the manufacturer guidelines regarding the torque limits.
- Depth control – use a measuring tape to monitor the depth of installation and ensure the anchor installs to the specified depth.
- Leveling and alignment – perform load testing to verify that the anchor meets the specified load-bearing capacity.
- Backfill – backfill the material used to the anchor to provide extra stability.
- Documentation – keep detailed records of the installation process including depth, torque values and any other relevant information.
Maintenance and inspection of no wrench screw anchor
Regular maintenance and inspection help to ensure long-term reliability and performance of the anchors. It can help identify and address potential issues before they turn to hazards and anchor failures. Additionally, it is advisable to adhere to industry best practices and manufacturer recommendations to ensure integrity and safety. The following is a basic guide for maintenance and inspection of no wrench screw anchors.
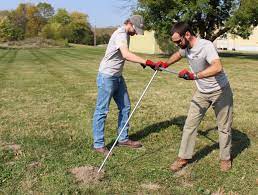
- Conduct regular visual inspections of the anchor and the surrounding area and check for signs of corrosion, damage or any unusual conditions.
- Apply protective coatings or using anchors made from corrosion-resistant materials.
- Remove any accumulated dirt, debris or vegetation from the anchor and its immediate surroundings.
- Periodically perform load testing to verify that the anchor continues to meet the specified load-bearing capacity.
- Schedule routine inspections based on the anchor’s application and environmental conditions.
- Visually assess the condition of the anchor and check for signs of corrosion, deformation or damage to the anchor shaft.
- Examine the soil around the anchor to ensure it remains stable and properly compacted.
- Inspect the supported structure for any signs of movement, settling or misalignment that may cause issues.
- Keep detailed records of inspections including dates, finding and any maintenance or actions taken.
Comparative analysis of no wrench screw anchor in Southeast Asia
A comparative analysis involves assessing and evaluating different types and designs of the anchors available. This helps to determine which type of no wrench screw anchor performs best in each soil condition. It also helps to ensure stability and load bearing capacity. The following are the common factors to include in a comparative analysis of the no wrench screw anchor.
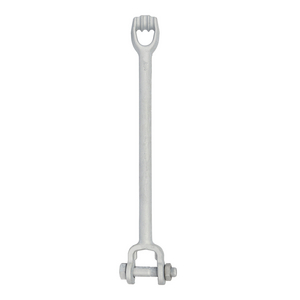
- Soil type and condition – Southeast Asia has a wide range of soil types such as sandy, clay, loamy and rocky soils. The no wrench anchor should perform best in each soil condition to ensure stability and load-bearing capacity.
- Load bearing capacities – compare the load-bearing capacities of different anchor types to meet project specific needs.
- Corrosion resistance – assess the corrosion resistance of anchor materials and coatings to increase durability.
- Environmental impact – the selected anchor should reduce soil disturbances during installations.
- Ease of installation – consider the ease of installation with reduce use of heavy machinery.
- Costs considerations – compare the overall cost of different anchor types including installation costs, labor and equipment requirements.
- Local regulations and standards – ensure the selected anchor complies with local regulations and standards in Southeast Asia.
- Project specific requirements – consider the specific needs of each project and select anchors that align with project requirements.
- Local supplier availability – evaluate the availability of anchor types and materials from local suppliers or manufacturers.
- Load testing – consider load testing and verification procedures to ensure that the selected anchors meet the specified load-bearing capacity.
- Environmental factors – evaluate the impact of factors like tropical storms, seismic activity and seasonal variations.
Certifications and standards in Southeast Asia
There are several standards and certifications that govern the use of no wrench screw anchors in Southeast Asia. These standards vary depending on each country in the region. Additionally, it is advisable to work with local authorities to ensure safe and reliable installations. The following are the standards and certifications for no wrench screw anchors in Southeast Asia.
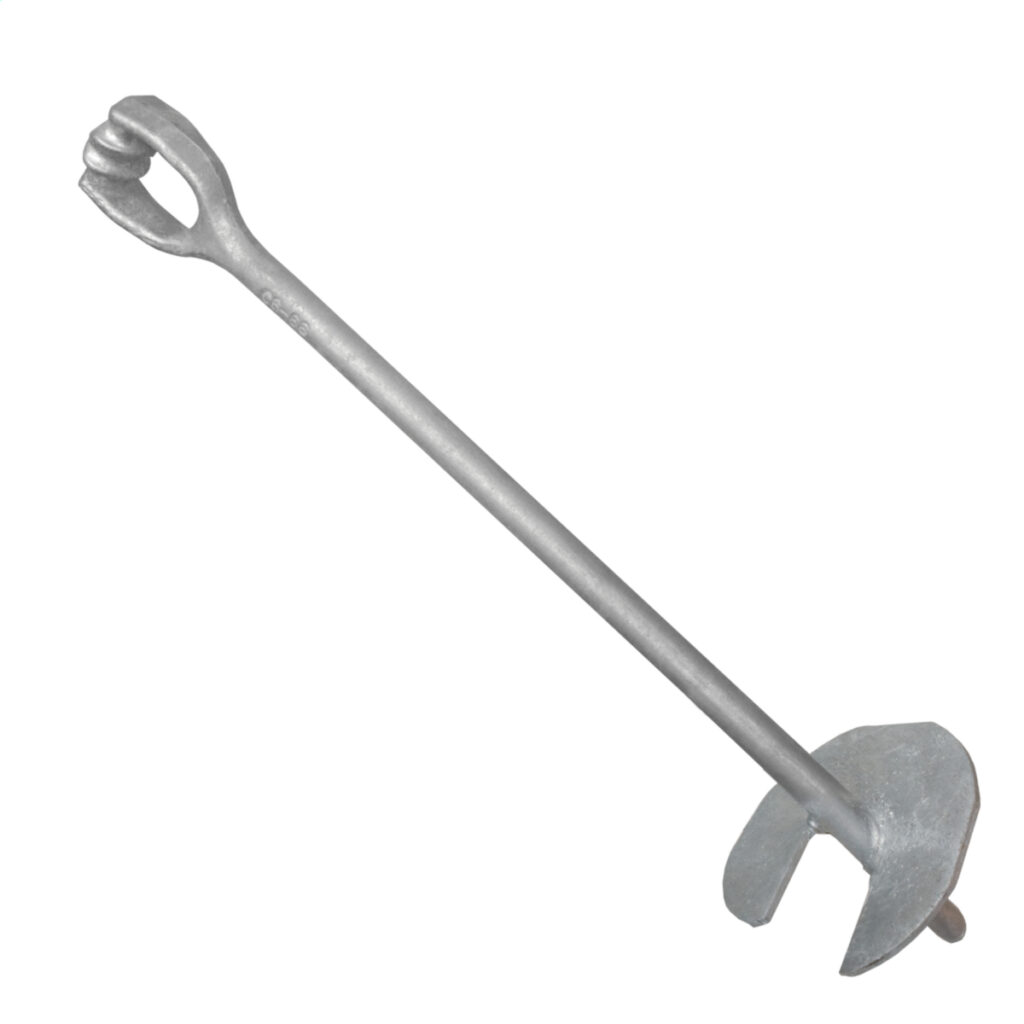
- ISO standards – these are certifications for manufacturers to demonstrate their commitment to quality and consistency.
- ASTM standards – this provides a range of standards related to helical screw anchors and their materials
- ASCE – this provides standards for design, installation and testing of screw anchors and helical foundations.
- Local building codes and regulations – these codes specify requirements foe anchor installation, load-bearing capacity and environmental considerations.
- Geotechnical engineering standards – this provides guidance on soil testing and anchor design based on local soil conditions.
- Safety standards – these helps verify the anchors meet safety requirements to protect workers and the public.
- Environmental standards – the project should adhere to environmental standards and regulations. This may involve reducing soil disturbance during installation.
- Local authorities – engaging with local authorities, engineering associations and regulatory bodies help determine the specific standards for your project.
Regional market for no wrench screw anchor in Southeast Asia
Various trends and development leads to increased demand for the use of no wrench screw anchor. This therefore affects the regional market for no wrench screw anchor in Southeast Asia. These factors include industrial growth, infrastructure development and urbanization. The following are the main factors that shape the regional market in Southeast Asia.
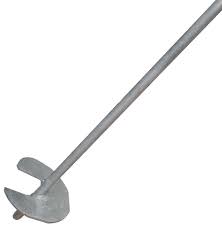
- Construction and infrastructure growth – economic growth includes residential, commercial, industrial and infrastructure projects. These require the use of strong anchors for increased stability.
- Renewable energy – the growth of project such as solar farms and wind turbines require the use of no wrench screw anchor for stability.
- Local manufacturing – local manufacturers may offer cost-effective solutions for regional projects in Southeast Asia.
- Imported products – the countries also import anchors from international manufacturers known for regional projects.
- Competition – competition between manufacturers and suppliers leads to innovation and cost effectiveness.
- Regulations and standards – the anchors should adhere to local regulations, building codes and industry standards.
- Maintenance and service – service providers offer anchor installation, maintenance and load testing services. This helps ensure the long-term reliability of anchoring solutions.
- Coastal and seismic zones – anchors providing stability in challenging soil and environmental conditions are high in demand.
Frequently asked questions
A no wrench screw anchor is an anchor with a helical design used to secure structures to the ground. They work by rotating into the soil to provide stability and load-bearing capacity.
No wrench screw anchor work in soil conditions such as sandy, clay, loamy and rocky soils.
Installation depth depends on factors like soil type, load requirements and project specifications.