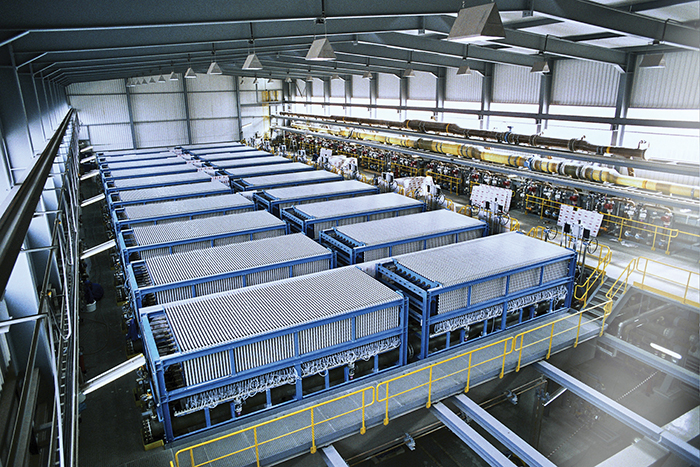
Chile is emerging as a global green hydrogen industry, given its abundant solar and wind resources. Electrolyzers play a crucial role in the development of green hydrogen for the energy transition. Electrolyzers split water into hydrogen and oxygen using renewable electricity. Chile will be able to count on its first electrolyzer factories after Corfo awarded US $25.6 million in financing. The project promoted by Corfo will allow the installation of plants in Chile with a total investment exceeding $50 million. Green hydrogen is crucial in Chile’s renewable energy sector. It replaces coal, natural gas, and diesel in mining operations. Electrolyzers depend on consistent and high-quality electrical current to split water through electrolysis. Conductor splices maintain the integrity of electrical connections, reduce resistance, and ensure optimal performance of the electrolyzer stack.
A well-designed conductor splice ensures minimal energy loss during transmission. This is crucial for the efficiency of renewable energy use in electrolysis. Chile is scaling up its green hydrogen production. This needs the reliability of electrolyzer components. High-quality conductor splices reduce downtime and maintenance costs. It supports large-scale deployment of electrolyzers. Conductor splices must be durable and resistant to environmental factors like temperature fluctuations, dust, and humidity to ensure long-term performance. This is crucial, as Chile aims to produce some of the cheapest green hydrogen to remain competitive in international markets. Conductor splices are crucial in integrating electrolyzers with renewable energy sources.
Key projects and their impacts in Chile’s renewable energy sector
Chile is advancing its green hydrogen sector by developing several key electrolyzer projects. The initiatives are expected to impact Chile’s energy landscape in various ways. Key projects include the AES Chile’s project Inna, a large-scale renewable hydrogen and ammonia production facility. These projects aim to harness the region’s renewable energy potential. Engie and Walmart Chile’s green hydrogen plant shows the practical application of green hydrogen in logistics and supply chain operations. These projects impact Chile’s energy sector through diversification of energy sources, decarbonization efforts, and economic growth.
The role of conductor splices in electrolyzer factories
Conductor splices ensure efficient and reliable electrical connections within electrolyzer factories. Electrolyzers need high-voltage, high-current electricity to split water into hydrogen and oxygen. Conductor splices help maintain electrical continuity, reduce resistance, and enhance system reliability. High-quality conductor splices prevent downtime, improve efficiency, and enhance safety. Common types of electrolyzers used in electrolyzer factories include compression splices, mechanical splices, and heat-shrink and cold-shrink splices. Their key roles include:
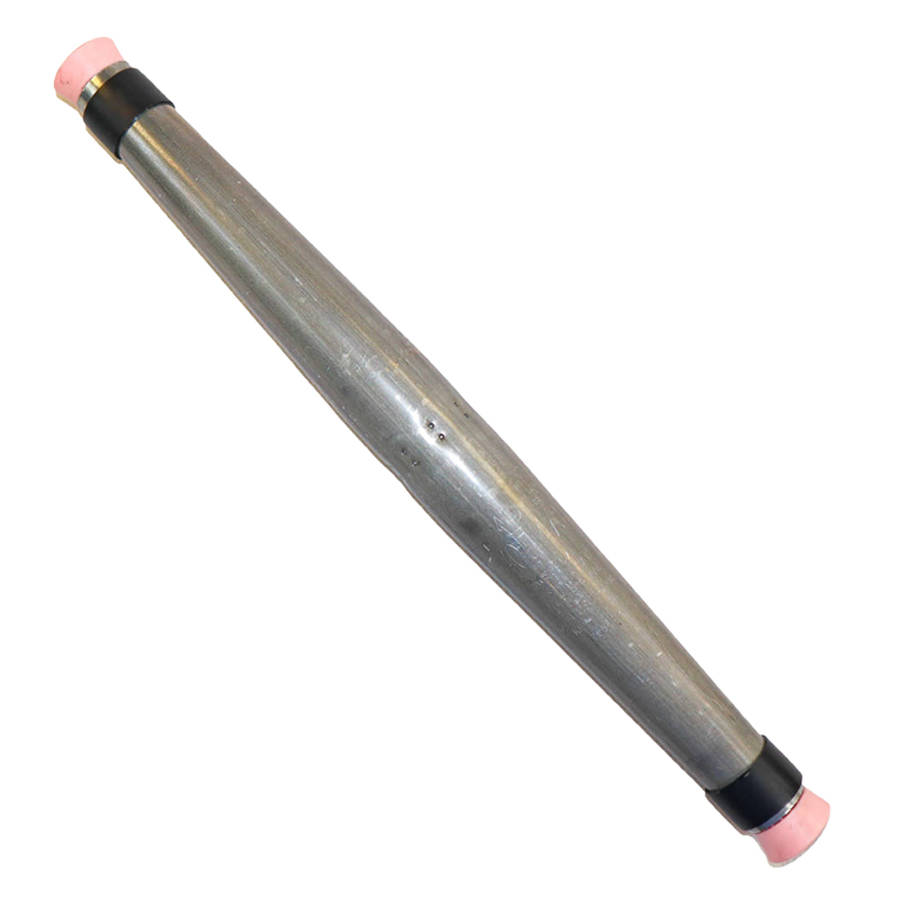
- Ensuring efficient power transmission—electrolyzers need consistent and high-power electrical input from renewable energy sources. Conductor splices help connect and extend power cables to ensure seamless electricity transmission.
- Reducing electrical resistance and energy loss—poor electrical connections can lead to voltage drops and overheating. High-quality conductor splices reduce resistance at connection points to ensure optimal energy flow.
- Enhancing system reliability—Electrolyzer factories operate in areas where vibration, temperature changes, and corrosion can affect electrical connections. Conductor splices provide durable, secure connections that prevent power failures and electrical hazards.
- Supporting modular electrolyzer designs—large electrolyzer plants have modular designs that need flexible expansion. The use of conductor splices allows new electrolyzers to integrate easily into these designs.
Technologies supporting Chile’s electrolyzer factories development
There are key advancements that ease the development of electrolyzer factories in Chile. With operations expected to start in 2026, electrolyzer technology supports innovations in energy, automation, and infrastructure. The success of the electrolyzer factories will depend on these technologies. They can enhance efficiency, scalability, and cost-effectiveness. Here are the key technologies.
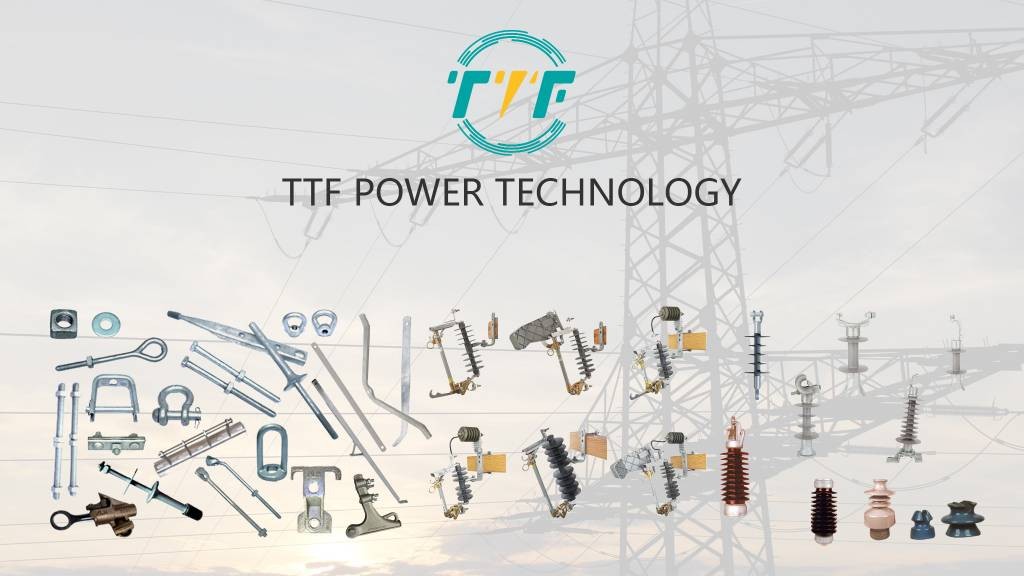
- Advanced electrolyzer technologies—these include proton exchange membranes, alkaline electrolyzers, and solid oxide electrolyzers.
- Renewable energy integration—this includes smart grid and AI-driven energy management and hybrid solar-wind energy systems. Conductor splices help n integrating these technologies into electrolyzer factories.
- Digital and automation tech—industrial IoT and predictive maintenance reduces downtime, extends equipment durability, and improves operational efficiency. Also, robotics increase production speed, reduce costs, and enhance quality control in electrolyzer factories.
- Hydrogen storage and distribution innovations—advances in hydrogen storage allow for safe and efficient long-distance transportation. Also, green hydrogen can be converted into ammonia and e-fuels to make it easier to store and transport.