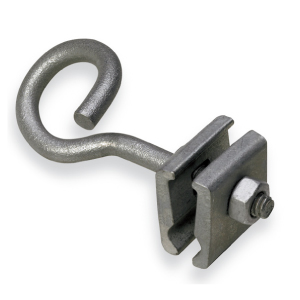
A span clamp is a hardware device used to secure and support electrical conductors between two points. It is also known as a suspension clamp or a mid-span clamp. Its purpose is to maintain the proper tension and spacing of conductors. This is conductors across spans between support structures. The clamps have designs to grip the conductor without causing damage. They also feature adjustable mechanisms to hold various conductor sizes and tension. Use of span clamps help to ensure the safe and reliable operation of overhead electrical lines. This is by providing mechanical support and preventing excessive movement. Span clamps are from durable and high-strength materials such as stainless steel or aluminum. They find use in applications such as telecommunications, power distribution and electrical installations.
Various uses and functions of span clamp
Span clamps have several uses and functions in electrical installations like overhead transmission and distribution. The clamps help to maintain overhead electrical transmission and distribution systems. This is to ensure the safe and reliable power delivery to consumers. The following are the various uses and functions of span clamps.
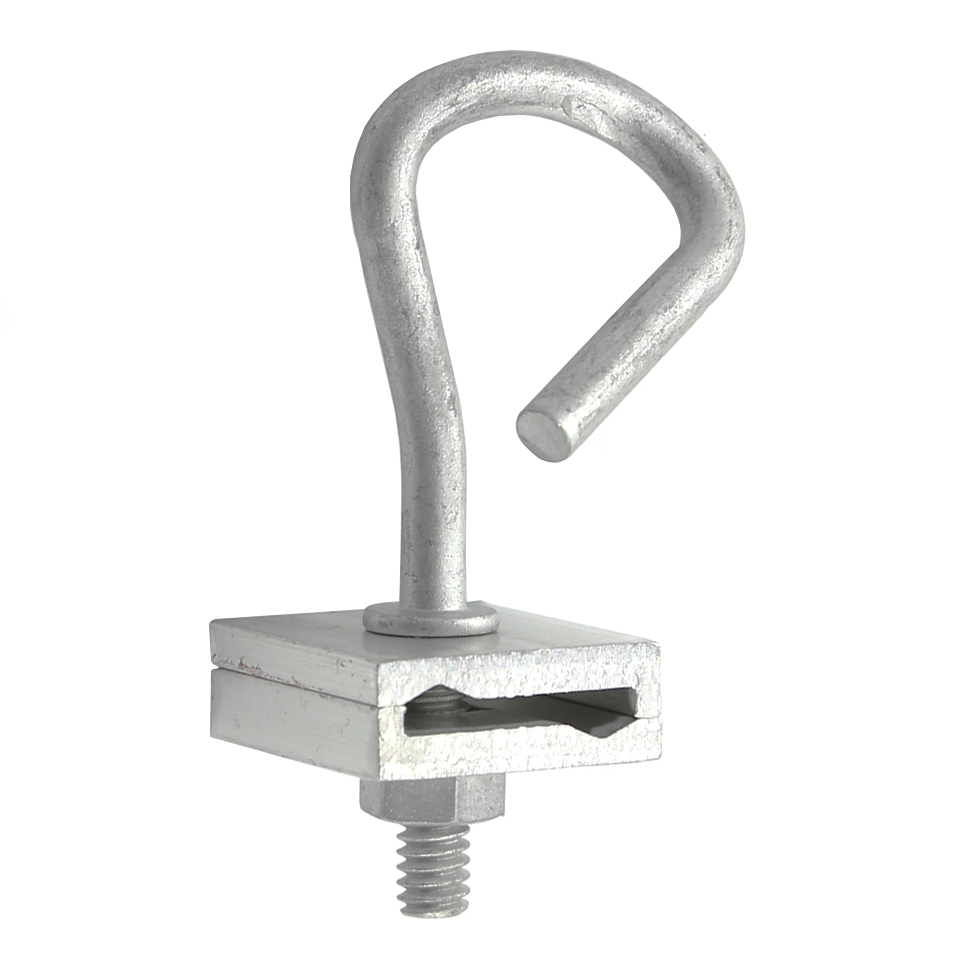
- Mechanical support – the clamps provide mechanical support for electrical conductors between support structures. This is by maintaining the proper tension and alignment of conductors over spans.
- Load distribution – span clamps distribute mechanical loads on electrical conductors across the span between structures. This helps to reduce the stress on conductors and support structures.
- Insulation support – mid-span clamps also use insulation materials to provide electrical insulation. This helps reduce the risk of electrical faults or failures.
- Corrosion resistance – span clamps are from corrosion resistant materials like steel or aluminum. These materials help the clamps to maintain the structural integrity of the clamps and extend service life.
- Conductor positioning – the clamps hold electrical conductors in place at specific intervals along the span between structures. This helps to ensure the consistent positioning and spacing to reduce electrical faults.
- Vibration dampening – the clamps have features that help reduce the transmission of vibrations along the conductors. This helps mitigate the risk of conductors’ fatigue and premature wear.
- Adjustability – this allows for easy installation and fine tuning of conductor tension. This ensures the conductors have proper tension and alignment
- Attachment points – the clamps serve as attachment points for extra hardware. This is including vibration dampers, spacer dampers. This is to allow for the integration of various components into the electrical system.
Types of span clamp
The types of span clamps depend on the on the regional standards, voltage levels and conductor types. Each type of the clamps has designs to meet specific requirements for different applications. Different power companies may choose their preferred types of clamps based on their specific requirements and regulations. The following are the main types of span clamps used on the power lines.
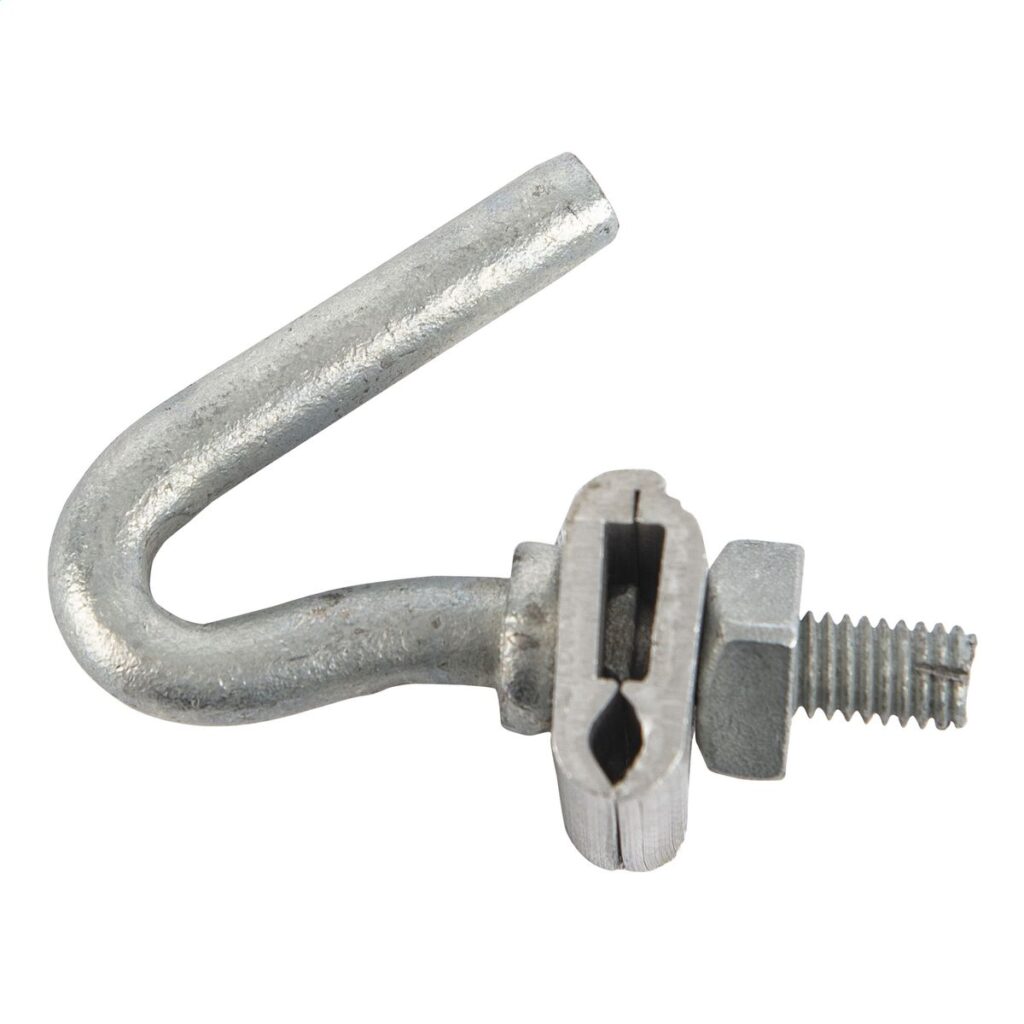
- Bolted span clamps – these clamps consist of two halves bolted together around the conductor. The halves are adjustable and provide a secure grip on the conductor without causing damage.
- Dead-end clamps – the clamps help to terminate the end of the conductor to a support structure. They have designs to withstand high mechanical loads and provide a secure attachment point.
- Strain clamps – these are clamps used to provide relief in overhead conductor spans. They install at points where the conductor changes direction. This helps to prevent damage to the conductor and support structure.
- Insulated span clamps – the clamps incorporate insulation materials to provide electrical insulation between the conductor and the support structure.
- Suspension clamps – the clamps hang to conductors from overhead support structures such as poles or towers. They have grooved surfaces to grip the conductor and distribute the load.
- Parallel groove clamps – these clamps connect two parallel conductors in electrical distribution. They provide a secure electrical and mechanical connection between the conductors.
- Saddle clamps – the clamps secure the conductors to support structures such as poles. They have a saddle-shaped design that grips the conductor from both ends.
- Guy wire clamps – these clamps secure guy wires to support structures and provide a secure attachment point for guy wires.
Classification for span clamps
Span lamps do not classify based on a single system but they categorize based on design, application and material used. Each category is for meeting specific applications based on various factors. These include load requirements, environmental conditions and compatibility with conductor type. Additionally, it is important to consider these classifications when selecting the span clamps. The following are the common categories of span clamp types.
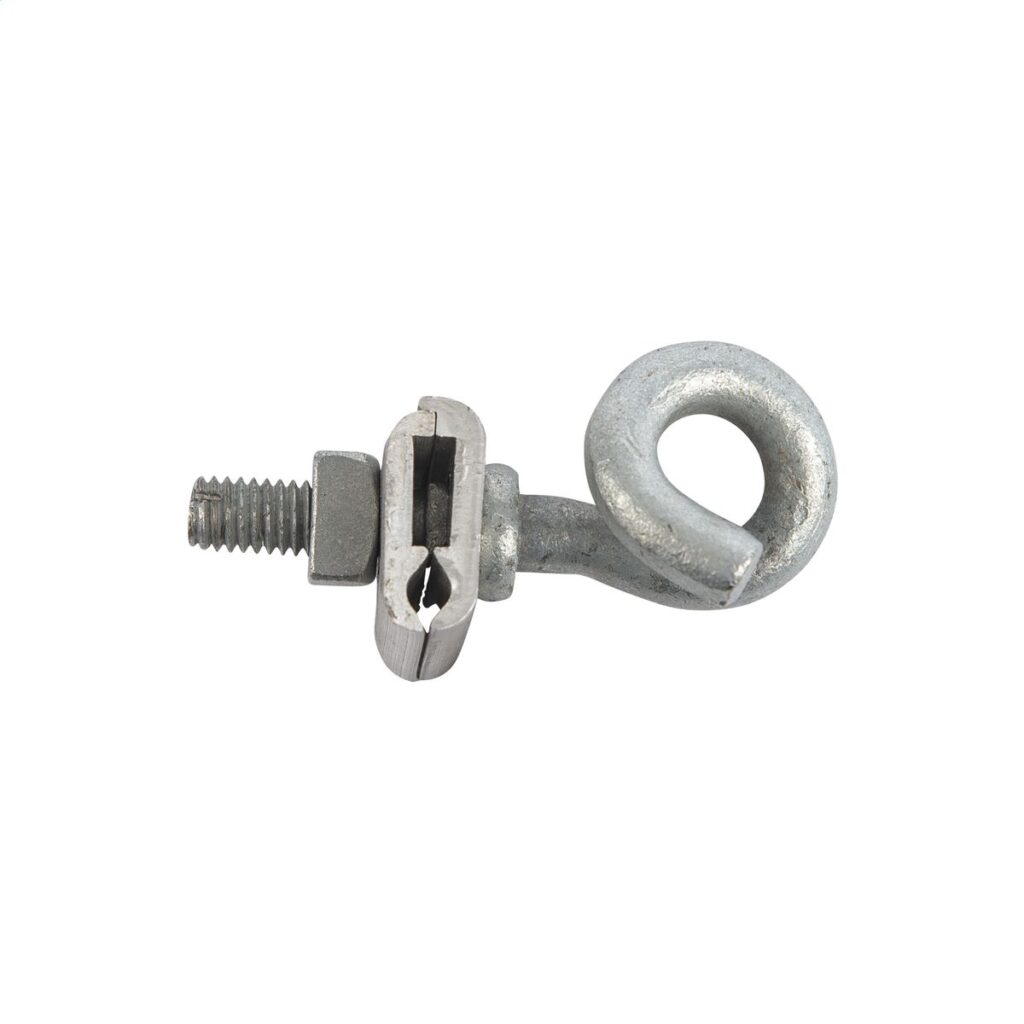
- By design – there are various types and designs of span clamps under this category. These are as discussed below.
- C-type – this is the most common type with a C-shaped body with a wedge gripping mechanism.
- E-type – this is like C-type but has a wider opening for larger diameter cables.
- O-type – this has designs to suit overhead ground wire applications. it has a rounded body with a groove for the cable.
- Q-type – this works for many drop wire take-offs featuring a body with many slots for individual wires.
- By application – there are various types of clamps that find use in different electrical applications. They find use in applications such as transmission lines, distribution lines, substation equipment and telecommunication lines.
- By material used – the span clamps are from various materials such as steel, aluminum or composite materials. These clamps increase strength, durability, corrosion resistance and electrical insulation.
Accessories used with span clamps
There are various accessories and components used with span clamp to enhance their performance. It also helps to provide extra functionality and ensure the reliability of electrical infrastructures. Additionally, it is important to consult with professionals for guidance on the best accessories to use with span clamps. The following are the common components used with span clamps.

- Spacer dampers – these install between adjacent conductors to maintain the least separation distance. It also helps to prevent galloping of the conductors during high wind conditions.
- Insulation covers – the covers install over clamps to provide electrical insulation between the conductor and the clamp body. They help prevent electrical contact between the conductor and the clamp.
- Corrosion protection – some of the clamps have corrosion-resistant coatings that protect them from exposure to outdoor elements.
- Weather protection – this is through the use of insulating boots or weatherproof covers that install over span clamps. They protect the clamps from rain, snow, UV radiation and other weather-related hazards.
- Vibration damper – these install along the conductor between span clamps to dampen the vibrations caused by winds. They help reduce the conductor fatigue and mitigate the risk of galloping.
- Mounting hardware – these include bolts, nuts, washers and bracket used to attach span clamps to support structures. They have designs to withstand the mechanical loads experienced by the span clamp.
- Grounding equipment – grounding clamps and connectors help to establish continuity and provide a path to ground for the conductor. They install at specified intervals along the conductor span and connected to grounding electrodes.
- Anti-theft devices – these include locking bolts or tamper-resistant fasteners used to secure span clamps. They also prevent unauthorized removal to help deter theft and vandalism.
Corrosion resistance properties for span clamps
Corrosion resistance is important in environments where there is moisture, humidity and salt.The properties helps to provide long lasting performance and reduce maintenance requirements. Also, it is important to consult with engineers for guidance on the corrosion resistance properties. The following are the corrosion resistant properties important for span clamps.
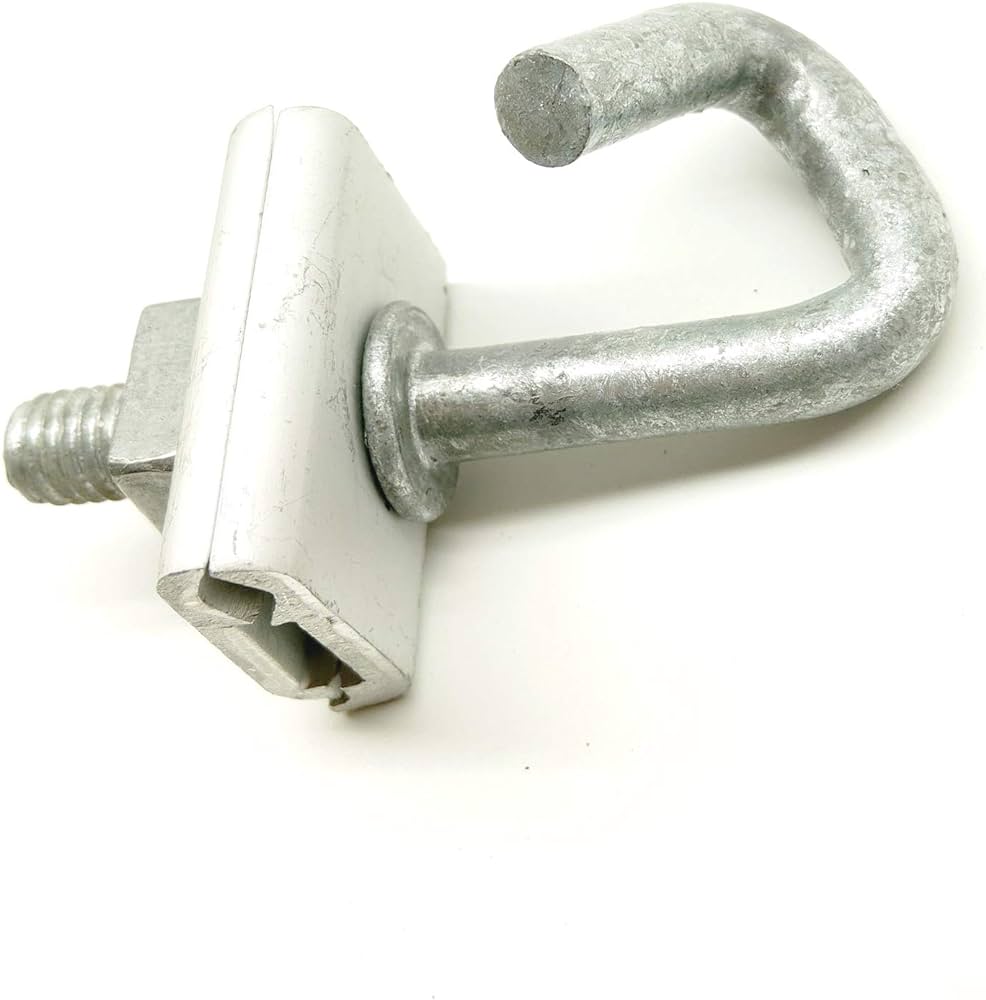
- Material selection – there are materials that are corrosion resistant for use in various applications. These include stainless steel, aluminum, galvanized steel or composite materials.
- Coatings and treatments – corrosion resistant coatings enhance the durability of the span clamp. Common coatings and treatments include zinc plating, epoxy coating, powder coating and passivation. Passivation is a chemical treatment process that removes free iron and other contaminants from the surface.
- Design considerations – the design of the span clamp influences their corrosion resistance. These include features such as smooth surfaces, rounded edges and drainage channels. They help to prevent the accumulation of moisture and debris to reduce the risk of corrosion.
- Environmental conditions – assess the specific environmental conditions where the span clamp will install. Consider factors like saltwater, industrial pollutants and atmospheric contaminants.
Frequently asked questions
Common accessories include vibration ampers, spacer dampers, conductor splices, insulation covers, mounting hardware and grounding equipment.
Design features such as smooth surfaces, rounded edges and drainage channels help prevent the accumulation of moisture and debris on span clamps. This is to reduce the risk of corrosion and improve performance.
Common types of span clamps include bolted span clamps, suspension clamps, dead end clamps, parallel groove clamps, strain clamps and saddle clamps.